|
 |
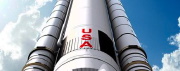 |
 |
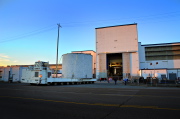 |
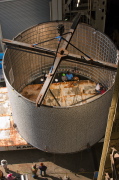 |
|
Interior of the Space Shuttle main tank, which has both ring and stringer stiffeners |
|
SLS takes on new buckling standards, drops Super Light alloy |
|
Transporting the 27.5-foot diameter orthogrid-stiffened cylindrical shell to NASA's test facility |
|
Arrival of the huge cylindrical shell at the location where it is to be crunched |
|
A view from above of the huge, internally orthogrid-stiffened cylindrical shell before installation in the test rig |
|
|
|
 |
 |
 |
 |
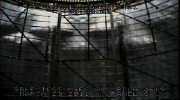 |
|
Two huge stiffened cylindrical shells being prepared by the NASA "SBKF" project for testing under axial compression |
|
Preparing for the Shell Buckling Knockdown Factor Test (2011) |
|
Test rig for buckling very large cylindrical shells under axial compression |
|
27.5-foot-diameter internally grid-stiffened cylindrical shell |
|
Buckling of a 27-foot diameter, internally orthogrid stiffened, uniformly axially compressed aluminum cylindrical shell |
|
|
|
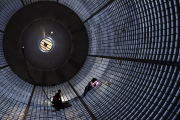 |
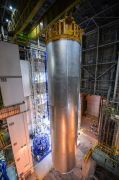 |
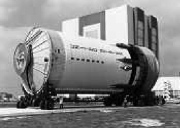 |
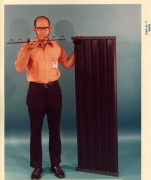 |
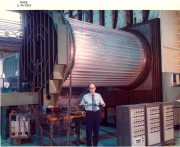 |
|
The assembled NASA liquid hydrogen tank for NASA's Space Launch System (SLS) |
|
NASA LH2 Qualification Tank for the Space Launch System (SLS) is prepared for testing |
|
Saturn VS II: A large cylindrical shell that is subjected to axial compression during launch into space |
|
Dr. Jerry G. Williams with composite hat-stiffened panel |
|
Dr. Jerry G. Williams with large stiffened cylindrical shell under combined axial compression, torque and bending |
|
|