|
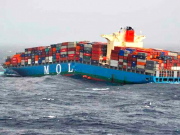 |
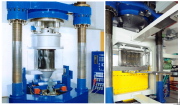 |
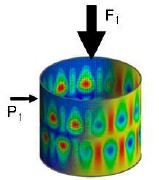 |
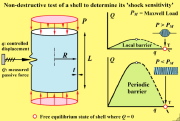 |
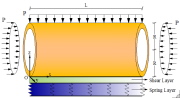 |
|
Shell plate buckling eyed in box ship break-up |
|
DLR’s buckling test facility: left: axial compression configuration; right: compression-shear- configuration |
|
The small load, P1, creates an imperfection that reduces the carrying capacity of the axially compressed cylindrical shell |
|
Non-destructive test suggested by J.M.T Thompson for buckling of an axially compressed cylindrical shell |
|
Hydrostatically compressed cylindrical shell on a Pasternak foundation |
|
|
|
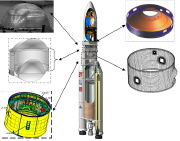 |
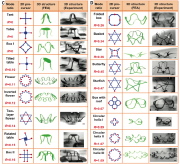 |
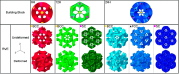 |
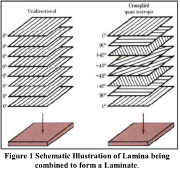 |
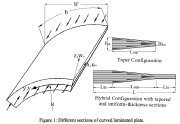 |
|
Some parts of a rocket that can buckle (DESICOS workshop: new robust DESign guideline for Imperfection sensitive COmposite launcher Structures) |
|
Assembly of micro/nanomaterials into complex, three-dimensional architectures by compressive buckling |
|
Buckling in 3D Structures investigated by the Bertoldi Group at Harvard University |
|
Schematic illustration of lamina being combined to form a laminate |
|
Buckling of axially compressed, curved composite shell containing tapered sections |
|
|
|
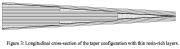 |
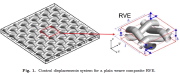 |
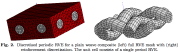 |
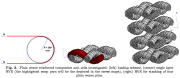 |
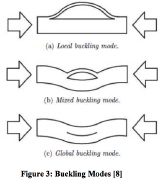 |
|
Detail of a tapered section including resin-rich layers |
|
Model used for the properties of a lamina in connection with multi-scale computational homogenization frameworks for the non-linear behavior of heterogeneous thin shells |
|
Finite element discretization of the lamina shown in the previous slide |
|
Building up a laminate consisting of layers modeled as displayed in the previous 2 slides |
|
Three modes of buckling of an axially compressed flat plate with a local delamination |
|
|